high-capacity
ladle
SCOPE
This case study involves a project where we were approached by a large steel producer to redesign a ladle to increase its capacity from 115 tons of liquid steel to 132 tons while reducing its weight by at least 5 tons. The new design had to be compatible with the existing installations in the factory.
APPROACH
This project presented a significant challenge, requiring the development of an innovative and efficient design that could increase the ladle's capacity while reducing weight and maintaining structural integrity.
To achieve this goal, we began by evaluating the existing ladle. A static assessment was conducted using ideal plastic, temperature-dependent material models, and a Gross Plastic Deformation (GPD) design check following the principles of EN 13445. Next, a fatigue assessment of all critical areas was performed. Non-welded areas were evaluated using FKM through post-processing the finite element results, while welded areas were assessed using hot spot analysis following IIW guidelines. This allowed us to determine the reliability of the present design and whether it could be used for the new design.
By iterating through multiple design options and simulations, still using the same static and fatigue evaluations, we developed a new ladle design by altering material grades, changing the refractory buildup, and virtually modifying the whole geometry, primarily by reducing thicknesses or removing ribs.
RESULT
The team successfully developed a new ladle design that met all requirements while maintaining structural integrity and reducing weight. Additionally, it was demonstrated that the new design had superior fatigue resistance compared to the existing ladle.
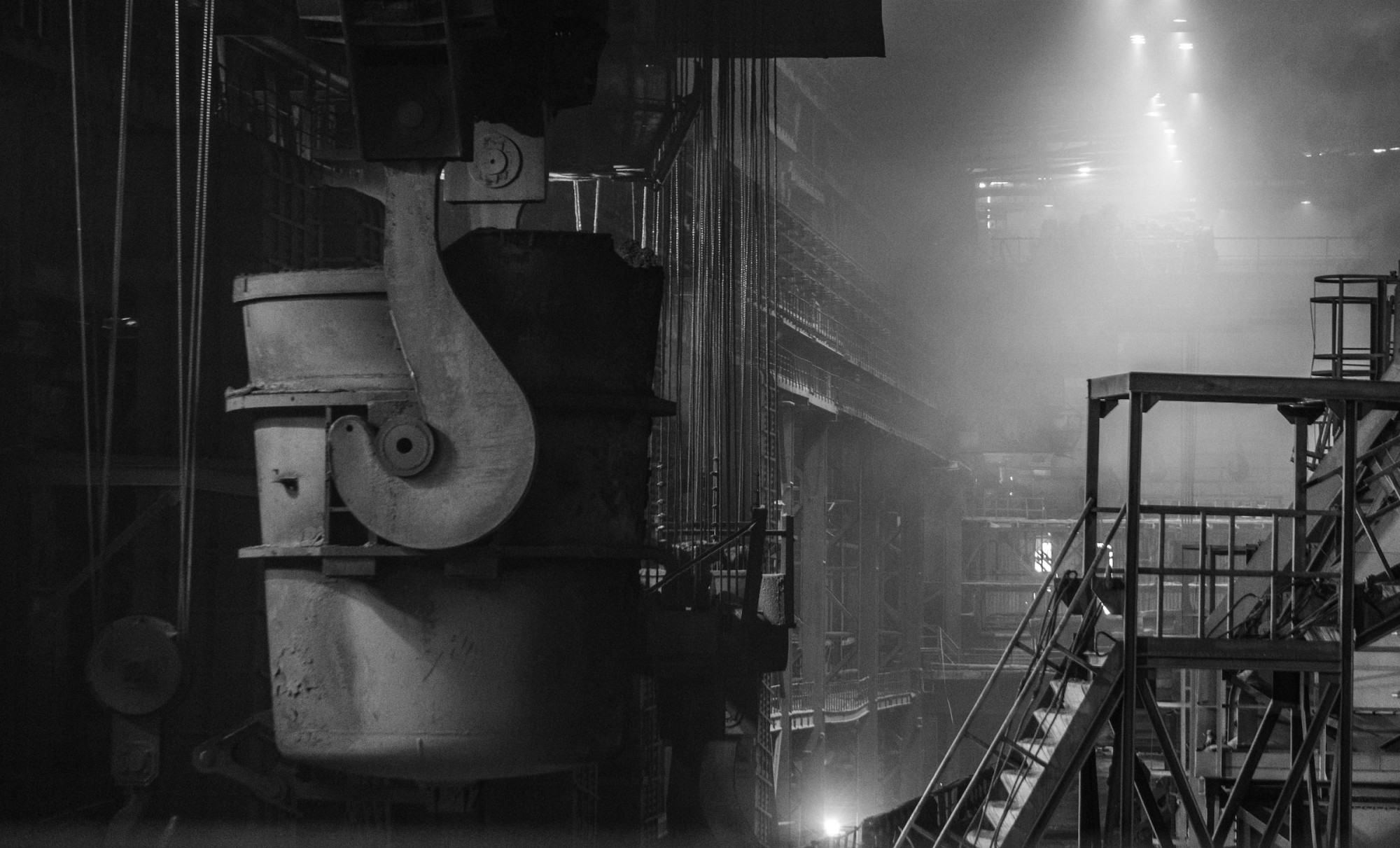

FE geometry and mesh of the ladle

A representative stress plot (left) and temperature distribution (right) in the ladle during operation